Top 3 types of vacuum chucks
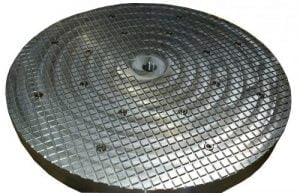
GRID & GASKET VACUUM CHUCK
Simply run the rubber gasket into the milled surface grid, trace the perimeter of your part shape. A secure way to hold irregular shapes.

Porous Metal Vacuum chuck
A porous aluminum is used for the top of this vacuum chuck. Great option to keep an even suction of thin flat parts.

Rubber mat vacuum chuck
The rubber mat vacuum chuck is a great choice for parts that are uneven. Small pores and suction cups in the mat allow part flexibility.
What is a vacuum chuck?
A vacuum chuck system uses vacuum suction to hold a workpiece in place while it is being machined or worked on.
It typically consists of a steel or aluminum vacuum table that has a series of small holes drilled through it, which is then connected to a special vacuum pump for vacuum chuck.
The workpiece is placed on the vacuum chuck, and the vacuum pump is turned on to create suction through the holes, holding the workpiece securely in place.
Vacuum chucks are commonly used in woodworking, metalworking, and other manufacturing processes where a secure hold is needed to work on a piece without damaging it.
Applications with a vacuum chuck include Milling, Surface grinding, EDM, Engraving and Polishing or just holding thin sheets of any material.
Braillon offer 3 common types of vacuum tables. Grid & Gasket, Porous Aluminum and rubber mat vacuum chucks.
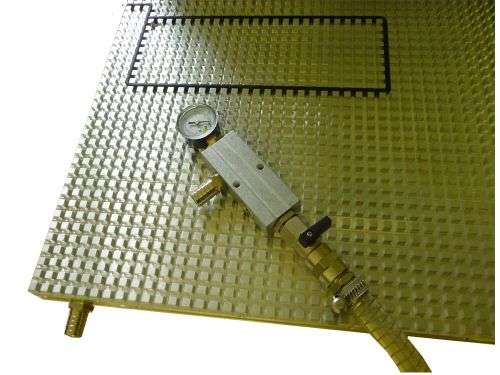
VRS GRID TYPE
Available in aluminum or steel. The VRS is atop of the line vacuum chuck that uses the grid and gasket system. Grid is milled in 12.5mm or 25mm spacing.

VRFP GRID TYPE
The VRFP grid is a round vacuum chuck. The circular shape of this vacuum chuck is a great option for rotary workholding.
Porous Metal Vacuum chucks

VMS POROUS TYPE
The VMS is a Sintered metal type vacuum chuck. It is Ideal for machining or holding thin elements (below 0.5 mm thick). Suitable for non-magnetic materials like glass, ceramics, plastic, rubber, thin sheets of any sort,
Rubber mat vacuum chucks
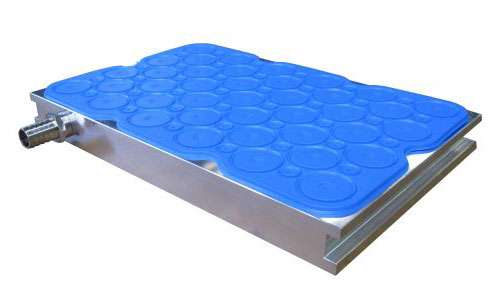
VMT SUCTION TYPE
The VMT vacuum chuck is made of aluminum, it uses rubber suction mats. Ideal for cutting out of steel or plastic sheet elements . Rubber mats is a consumable item.

VMR SLOT TYPE
The VMR uses a blank rubber mat on top of it. Holes are made in the rubber mat where the part will be in contact. Great flexibility and simple to setup. Rubber mats purchased separately.
Things to keep in mind...
Vacuum workholding is a popular method for holding thin and flexible workpieces that cannot be easily held with vises or clamps. However, there are certain tips and guidelines to follow when using vacuum workholding to ensure that the workpiece remains securely held in place during machining operations.
Firstly, it’s important to understand that vacuum power has an upper limit. The maximum vacuum power any vacuum pump can achieve is 14.9 pounds per square inch at sea level. This is because the weight of air around us is what actually pushes the part down onto the chuck.
Vacuum workholding is often a secondary choice, and vises and clamps are the preferred method of holding a workpiece due to theoretically unlimited clamping force. However, thin parts are not easily held with a vise, and a vacuum chuck may be your only choice. But don’t expect to be able to machine a part as aggressively as when using a vise.
When using vacuum workholding, use common sense. Short and wide parts that absolutely cannot be held with a vise are the best candidates for vacuum workholding. However, holding a part that is 1 inch square and 4 inches tall is not going to hold up against cutting forces.
To maximize sideways rigidity, use workstops whenever possible. Side loads are the enemy of vacuum applications! Adding pins, side rails, or cutting a shallow pocket in one of our customizable Top Plates for the part to sit in will help.
Using small cutters when possible and sharp cutters will help reduce side forces and the chance of sliding a part off the chuck. Small cutters exert less torque, reducing side forces, thereby reducing the chance of sliding a part off the chuck. Sharp tooling naturally exerts lower side loads, which reduces the chances of a part sliding on a chuck.
Flexible workpieces might be problematic because the rigidity of the workpiece helps maintain a vacuum seal. Very thin or very soft materials may be more likely to flex at the edges and peel off the vacuum chuck. Have adequate coolant or air to help with chip evacuation since chips are forced downward. Machine a clearance trough in a Top Plate along the edge of the cut so chips have a place to go. Outside corners have minimal support, so slow down. Inside corners have good part support but more of the tool is engaged in the cut, so side loads are higher than normal, so slow down